Content
- What Are The Main Problems With A Jit Just In Time Production Strategy?
- Make The Most Of Boms With An Erp System
- Sap Business One
- Product
- Bill Of Materials Software Buyers Guide
- Deltek Costpoint
It would also specify the correct order of steps needed to cut the wood, assemble the casing, and paint it. Finally, the bill of materials would specify the labor and machine requirements for that step of the assembly. We searched and searched, but we couldn’t find any products in our database that match your criteria. They’d be happy to provide a list offree bill of materials software recommendationsthat meet your exact requirements. It can be argued that backflush accounting simplifies costing since it ignores both labour variances and work-in-process.Continue to add to and refine the list, tracking all changes. Choose the BOM presentation, such as single- or multi-level, that makes sense for the product. For the BOM to continue to provide value and remain accurate, all changes need to be tracked. For a new product, an MBOM may last for a set period, such as several weeks. Then, if it becomes clear the product requires changes, the MBOM can be updated or a new one may be generated. An implosion display is the inverse of an explosion display. It starts with individual parts and links them to form the major product or assembly.
What Are The Main Problems With A Jit Just In Time Production Strategy?
Choices typically include purchasing the part, producing it internally or having it manufactured by subcontractors. The quantity indicates how many of each part will be used in an assembly or sub-assembly. They’re generally easier to generate and likely to remain accurate for longer periods.
What is another common name for the bill of materials?
A bill of materials or product structure (sometimes bill of material, BOM or associated list) is a list of the raw materials, sub-assemblies, intermediate assemblies, sub-components, parts, and the quantities of each needed to manufacture an end product.For example, an EBOM may list parts related to a specific function of the product, such as chips for a circuit board. An MBOM, by definition, lists every material that goes into manufacturing a product.
Make The Most Of Boms With An Erp System
A disadvantage of MES is that it is not suitable for small series or prototype production. Such type of production should be segregated from the series production and mass production. Multilevel BOMCreate profiles for items in the system that can then be combined to create a completed project. BOM software ensures that all subassemblies and component parts are listed in the system for accuracy.Routing managementDetermine the best machines and equipment to use for a specific project. Takes into account the characteristics of each production asset to automatically distribute the work in the most efficient way possible.Cost maintenanceCalculate costs for each item in a bill of materials. This tool can multiply the cost by quantities needed and factor in any other costs, such as tooling or overhead operational costs.Change historyTrack fluctuations in the availability and cost of materials and parts.
- For example, SAP S/4HANA allows companies to create advanced versions of BOMs for complex assemblies and speed up time to market through specification of work center details within a BOM.
- For instance, wiring and lumber generally are purchased by the foot.
- The system multiplies the Run Labor value in the Routing Master table by crew size during cost simulation to generate total labor dollars used in the cost simulation.
- This helps ensure they meet customer expectations and is critical when products need to meet safety or other standards.
- Bill of materials software breaks the manufacturing of an item down to the component level.
Audits and compliance problems can cause big headaches for manufacturers. With a BOM system, every change to items or the production process is recorded and saved, so documents proving compliance are always on-hand. With hundreds of options for manufacturing systems, it can be challenging to identify the capabilities you need and find the vendors that best meet your requirements. This Buyer’s Guide is designed to give you the information you need to make the best decision for your business quickly. Accuracy of production and consistency characterize strong manufacturing operations. Like a good recipe, each item on a bill of materials needs to be exactly right to produce high-quality end products while maintaining equipment effectiveness and production rates. Conversely, neglecting to create a BOM or failing to update one can result in inaccurate product costs, products being made incorrectly, inventory overages or shortages and production delays, among other challenges.A quality BOM software will let you find the exact materials needed to complete an assembly, or suggest possible alternatives via search tools within the program. You can also look at release status and life cycle, and monitor revision history for any changes that do occur within your bill of materials. For fixed quantity components, the Work Order and MRP systems do not extend the component’s quantity per assembly value by the order quantity. ACQ is used as a divisor by the cost rollup for fixed components. Review your bills of material to understand the bills’ input to your material product costs.Optimizing accuracy and quality from the beginning of the process allows manufacturers to increase production volume and scale the business. Many still rely on Excel, but manufacturing systems and ERPs with BOM functionality help companies manage and automate this important task. This becomes crucial when working with multiple teams, sites and service providers on the same project.For a finished product, there may be more than one engineering BOM created. There are different types of bills of materials specific to engineering used in the design process; they’re also specific to the manufacturing used in the assembly process. Yield %Represents the planned output yield percent for a step. The Planned Yield Update program uses this value to update the Cumulative Percent in the bill of material and the Operation Scrap Percent in the routing. Materials Requirements Planning uses the step scrap percent and the existing component scrap percent to plan component demand.Cum %Represents the cumulative planned output yield percent for a step.Oracle Autonomous Database can automate routine administrative and operational tasks for DBAs and improve productivity, but … SAP offers well-known functionality to create various BOMs. Legacy users have been able to use BOMs created through SAP R/3 and ERP Central Component, and SAP HANA continues that functionality. Accounting Learn about accounting tools, methods, regulations and best practices. Today, ERP also encompasses business intelligence and front-office functions like ecommerce. Companies of all sizes and across all industries use ERP solutions.
Sap Business One
Backflush accounting is inappropriate when production process is long and this has been attributed as a major flaw in the design of the concept. It may also be inappropriate if the bill of materials contains not only piece goods but also many parts with more or less variable consumption. Difficulties maintaining correct inventories on shop floor may also appear if it is usual practice to use alternative materials and/or quantities without needing derogation.
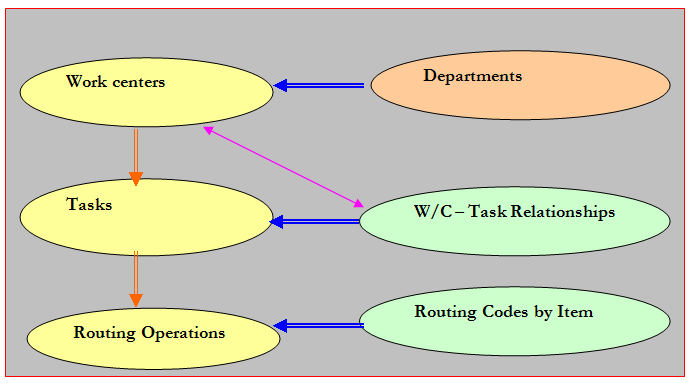
Some basic parts, like adhesives, may be used in multiple areas. A BOM is essentially a blueprint for manufacturing a product. It encompasses the materials, components and steps required to create the item. Material requirements planning is among the first software-based integrated information systems designed to improve productivity for businesses. Creating an accurate bill of materials is vital because it ensures that parts are available when needed as well as ensuring that the assembly process is as efficient as possible. A bill of materials is a centralized source of information used to manufacture a product.
Product
By helping ensure the right parts and materials are available at the right time and in the right quantities, BOMs help manufacturers remain within budget and on schedule. At the top is the completed product, next are subassemblies and below those are the components and materials that go into making the product. This includes details like part names, numbers, descriptions and the quantities needed.
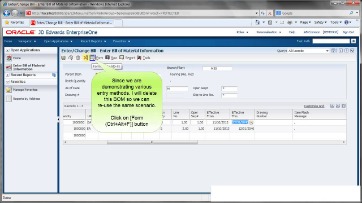
This BOM is used for finished products that are configured and designed to meet specifications requested by a customer. It identifies the materials and components, including any labeling or packaging requirements, needed to manufacture the product to the customer’s requirements.It is a list of the items needed to create a product as well as the instructions on how to assemble that product. Manufacturers that build products start the assembly process by creating a BOM. For example, the outer casing assembly might include a materials list including the wood for the casing, screws, and paint.Users can create item profiles for every part that goes into a specific product, then use these to create multiple lists for a single product to show subassemblies. A bill of materials is the record of the raw materials, sub-assemblies and supplies used to construct a product.If the product fails, a single-level BOM makes it difficult to determine which part needs to be replaced or repaired. An engineering BOM is developed while a product is being designed and defines a finished product’s original design. It includes the items, parts, components and subassemblies as designated by engineering. It generally consists of a technical drawing of the product.When each production run follows the same BOM, the products themselves remain consistent. This helps ensure they meet customer expectations and is critical when products need to meet safety or other standards. The bill of materials is used to calculate the cost of a product, as well as to order parts from suppliers. It is an essential requirement when an organization is using a material requirements planning system. A BOM list is necessary when building a product and ordering replacement parts, and reduces possible issues if product repairs are required. It helps to plan for acquisition orders and reduces the possibility of errors.

In many organizations, different departments or functions use different information systems. For the BOM to remain accurate and up-to-date, it will need to assemble information from all these systems into a single record. Engineering BOMs, as their name indicates, typically are developed by engineers. They often use computer-aided design software or similar systems to create the BOM. For instance, assume a BOM for a vehicle is constructed in a single-level format. It later becomes clear that the door handle on the vehicle is faulty. The single-level BOM won’t distinguish between the parts that went into the handle and those used in other vehicle parts.You can set rates per unit, per 10, per 1000, and so on.The system uses the values in the Description-2 field on the User Defined Codes screen for costing and scheduling calculations. The description is what the code represents, but is not used in calculations. Operation Scrap %The system uses this value to increase or decrease the amount of materials to account for loss within the operation. The system updates this value on Enter/Change Bill of Material when you run the Planned Yield Update program. The system calculates this value by compounding the yield percentages from the last operation to the first operation. Use a processing option in Enter/Change Routing to enable the system to calculate the component scrap percent. FieldExplanationBill TypeSimulated Rollup will only cost an “M” type BOM.Backflush accounting is employed where the overall business cycle time is relatively short and inventory levels are low. Shrink is the expected loss of parent items due to the manufacturing process. Shrink and scrap are compounded to figure the total loss in the manufacture of a particular item.The system uses this value to adjust the operation step scrap percent for the components at that operation step. This enables the MRP system to use the operation step scrap percent along with the existing component scrap percent to plan component demand. ERP systems offer a holistic view of operations, so many companies, including manufacturers, are adopting these platforms to manage the front and back end of the business. An MRP offers similar functionality with a focus on manufacturing, while most other manufacturing systems, such as a manufacturing execution system , can integrate with an organization’s existing ERP. In a nutshell, it is the complete list of all the items that are required to build a product.