Content
- Example Of How Prime Costs Work
- Prime Costs Vs Conversion Costs
- How To Calculate Single Overhead Rate
- 2 Explain And Identify Conversion Costs
He is also an educational consultant who coaches students to equip with relevant knowledge on entrepreneurship and helps them to set up small-scale and freelance businesses. Without knowing the beginning inventory, one cannot accurately calculate Inventory Turnover Rate and Inventory Days of an organization. Let’s consider that the cost of goods sold is $5,000, ending inventory is $10,000 and purchases made are $3,000 in the financial year 2019. Harold Averkamp has worked as a university accounting instructor, accountant, and consultant for more than 25 years. He is the sole author of all the materials on AccountingCoach.com. A variable cost is an expense that changes in proportion to production or sales volume. David Ingram has written for multiple publications since 2009, including “The Houston Chronicle” and online at Business.com.

Direct labor cost amounted to $200,000 and factory overhead is estimated at $250,000 based on direct labor hours. Direct labor, as mentioned above, refers to the salaries of production workers. Factory overhead refers to costs incurred in production other than direct materials and direct labor.
Example Of How Prime Costs Work
The examples of period costs are legal costs, promotion costs, administrative costs and sale commissions. Period costs are recorded in the profit and loss statement of an organization. There is no standard formula for calculating the total period costs. One can arrive at total period costs by closely monitoring and reporting the expenses that aren’t related to manufacturing a product.The calculation for prime costs includes the amount spent on both direct materials and direct labor. Tangible components—such as raw materials—necessary to create a finished product are included as a part of direct materials. For instance, the engine of a car and the spokes of a bicycle are included in direct material costs because they are each necessary to complete the production of that specific item. Manufacturing overhead consists of fixed expenses specifically related to the manufacturing component of a business. Electric utilities in an assembly-line facility count as manufacturing overhead, for example, while the same utilities used in a manufacturer’s sales office do not. Manufacturing overhead can also include full-time salaries for production workers. Manufacturing overhead is relevant to the concept of conversion costs because it is a vital component in the conversion of raw materials into finished goods.
Prime Costs Vs Conversion Costs
Bruce’s Bike Company is a bicycle manufacturer that specializes in high-end 10-speed bikes. Bruce is trying to figure out what his conversion costs are for the quarter in order to estimate his finished inventory for theinterim financial statements.
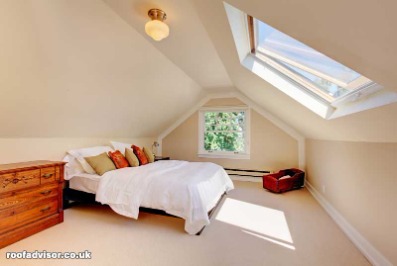
Direct labor costs are the wages paid to the employees engaged in manufacturing a product or provision of service. For example, wages or salary paid to the workers at the shop floor environment come under direct labor costs. A shop floor is the production area where people work on machines. Manufacturing overheads are the indirect costs incurred while manufacturing a product. Prime costs include the expenses that directly relate to creating finished products. Conversion costs, on the other hand, are expenses that a company incurs in converting raw materials into a finished product.
How To Calculate Single Overhead Rate
Thus, we can get conversion costs if we subtract direct material from total manufacturing costs. Notice that the actual costs of the necessary raw materials are not included in conversion costs. But we want to focus on what is included in conversion costs, so let’s look into what makes up direct labor costs and manufacturing overhead costs. The true cost a company uses in the process of turning raw materials intofinished goodsincludes both overhead and direct labor.
What does overhead mean?
Overhead refers to the ongoing business expenses not directly attributed to creating a product or service. … In short, overhead is any expense incurred to support the business while not being directly related to a specific product or service.Manufacturing overhead costs are things like indirect labor, utilities, supplies, equipment, insurance, taxes, tools, and regulatory obligations. While prime costs and conversion costs are closely related, they are not the same.
2 Explain And Identify Conversion Costs
The formula is relatively straightforward, and the variables in the equation are not too difficult for managers to find. Look for manufacturing overhead figures in the expense records of your accounting system. Search for direct cost figures either from your expense records or your purchasing records for the period. In accounting, conversion costs are important for balance sheets and income statements.Conversion costs consist of both overhead costs and direct labor.Overhead costsare expenses used to produce products that can’t be attributed directly to a production process. Factories must use electricity to power their machines and produce products, but each dollar of electrical costs can’t be directly tied back to the products that were produced. Prime costs are reviewed by operations managers to ensure the company has an efficient production process. The calculation of prime costs also helps organizations set prices at a level that produces an acceptable amount of profit. Management needs to understand its costs in order to set prices, budget for the upcoming year, and evaluate performance. Sometimes individuals become managers due to their knowledge of the production process but not necessarily the costs. Managers can view this information on the importance of identifying prime and conversion costs from Investopedia, a resource for managers.Organizations should also calculate prime costs, in addition to conversion costs, to understand the efficiency of the production environment. Prime costs refer to all the direct expenses related to producing a finished product. Prime costs include direct material costs and direct labor costs.
What Does Manufacturing Overhead Have To Do With The Total Conversion Costs?
As said above, the conversion cost is the combination of manufacturing overheads and direct labor. Thus, its formula is Direct Labor Plus Manufacturing Overheads cost. Overhead costs are the expenses that a company incurs in manufacturing the product. But, one can’t directly attribute these expenses to a production process. Examples of manufacturing overhead are depreciation, utilities, rent, testing, and more costs that a company incurs within its manufacturing facilities.
- Without coverage of overhead expenses like utilities and taxes, operations can come to an abrupt standstill.
- Prime costs are reviewed by operations managers to ensure the company has an efficient production process.
- A point to note is that one may exclude individual costs from the calculation of conversion costs if a business does not incur them regularly.
- Notice that the actual costs of the necessary raw materials are not included in conversion costs.
- Managers also use these costs to evaluate the efficiency of the production process and identify waste.
Prime costs refer to the total cost of direct materials and direct labor. Enter the total direct labor cost and the manufacturing overhead into the calculator to determine the conversion cost. Conversion costs include all direct or indirect production costs incurred on activities that convert raw material to finished goods. Direct labor costs may seem to be pretty straightforward; however, these costs don’t just include wages. You want to tally all of the costs that must be paid for the labor needed to actually manufacture a product. Direct labor costs should also include all of the expenses necessary to hire and retain an employee who physically works to turn the raw materials into a product.Manufacturing overhead costs are those manufacturing costs necessary to produce a product, excluding the direct labor costs. This includes indirect labor costs, which are labor costs incurred by a company for those employees who are not directly involved in producing the actual good. Examples of employees in this category are managers, nurses, security guards, janitors, cooks, maintenance workers, accountants, executives, trainers, parking attendants, and secretaries.
The Significance Of Inventory Turnover Ratio
For example, if a painter was hired to paint the car being created, the wages paid to the painter would be included in the prime costs. Conversion costs allow managers and other supervisors to accurately measure and keep track of the expenses of production. Conversion costs can also be used in the development of product-pricing models as well as when estimating the end value of finished products. Business owners or managers may also look at conversion costs to determine if there is waste that can be eliminated and to better understand the efficiency of their production process. In the conversion cost calculation, direct labor refers to money spent on employees or other workers who directly work on production. For example, the salaries of the employees who are responsible for manufacturing goods, such as machinists or assembly-line workers, are considered direct labor costs. If you hire contract workers for a particular project, the wages you pay them would also be counted as direct labor expenses.Prime costs include both direct materials and direct labor expenses that are required to create complete products. Direct materials include the purchase of raw materials or any tangible part that is needed to complete a product. For example, the axle of a car would be considered a direct material because it is required to build a complete car. Conversion costs are also used as a measure to gauge the efficiencies in production processes but take into account the overhead expenses left out of prime cost calculations. Operations managers also use conversion costs to determine where there may be waste within the manufacturing process. Direct labor costs include only costs related directly to the workers who took part in the creation of finished products.
Direct Labor Costs
So direct labor costs appear commonly in both prime costs and conversion costs. Conversion costs is a term used in cost accounting that represents the combination of direct labor costs and manufacturing overhead costs. In other words, conversion costs are a manufacturer’s product or production costs other than the cost of a product’s direct materials. In a processing environment, there are two concepts important to determining the cost of products produced.Conversion costs take all costs related to manufacturing processes into account to pinpoint opportunities to reduce costs and improve profit margins. As such, calculating conversion costs in your manufacturing operation can provide distinct competitive advantages.The overhead costs that are part of conversion costs are any expenses that aren’t directly tied to the production of inventory but that are still necessary. For example, the cost to maintain the equipment that produces goods would be considered an overhead cost. Therefore, once the batch of sticks gets to the second process—the packaging department—it already has costs attached to it.