Content
- Business In Action 4 3
- Equivalent Units Of Production
- How To Create A Business Brief With Example And Template
- Definition And Explanation Of The Concept Of Equivalent Units
- Apply Formula To Calculate Equivalent Units Of Production For Materials, Labor And Overhead Costs Or Conversion Costs
Plugging in the information that you have from the parts maker, there are 300 partially completed units. The accountant first finds out how many units have been finished and sent out. Since these items are 100% complete, each unit sent out is one equivalent unit of production. At the end, he determines that his 100 units are only 70 percent the way through the production process.
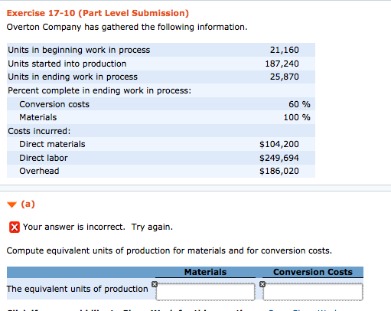
To calculate this, the accountant would multiply the number of items in progress by the percentage of work done on them so far. Segment reporting allows management to assess the profitability of divisions or product lines. In this lesson, you will learn how to prepare a segmented income statement and use the information to make decisions. Cost-volume-profit analysis is one way for management to determine the relationship that exists between a company’s costs, its revenue, and its sales volume. In this lesson, we’ll take a look at how a restaurant might use CVP to look at its revenue. Are those costs incurred to convert raw materials into the final product .This involves deducting the closing work-in-progress from the amount introduced in the process during the current period. For example, the closing stock of 200 units in a process, with 60% complete in respect of materials, wages, and overheads, is equivalent to 120 units (i.e., 200 x 60%), which are 100% complete. Work-in-progress can be valued based on actual cost (i.e., an attempt may be made to find out how much materials have been used on the incomplete units and how much labor and expenses were used). Note that, in the weighted average method, beginning work-in-process inventory is ignored. When you use weighted averages, all work accomplished in prior periods is not factored into the equations. This lesson will discuss manufacturing costs in a job order costing system and demonstrate the proper recording and recognition of manufacturing and period costs through journal entries. This lesson will review the process costing system and discuss how manufacturing companies track the flow of expenses through departments involved with the manufacturing process.
Business In Action 4 3
The long and short of it is, the equivalent units of production is an indicator of how much work was done by a manufacturer who has partially completed products in process at the end of a designated period. Maybe that wasn’t so “short”, but it’s a weird and semi-complex term to understand. Basically, all of the work-in-process inventory at the end of a period is expressed as fully-completed units which gives us the equivalent units of production. If you’re a new business, it might be beneficial to take the course Business Accounting for Start-ups to familiarize yourself with these terms and concepts. They can then calculate the equivalent units of production that were needed to finish these items. Managerial and cost accountants use the equivalent units of production to allocate production costs to units during the manufacturing process. For instance, calculating the cost of goods produced is simple if there is no beginning or endinggoods in process inventory.Thus, Pat’s equivalent units of production for the period is 70 EUP. Calculate the units of production from both materials and conversion. Using FIFO, you’ll have two percentages to determine for beginning and ending inventory. A manufacturing company must accumulate costs from three categories when determining the final inventory cost, which could be calculated using a job-order or process costing method. The units that remain in the ending work-in-process inventory, however, are not complete. Therefore, to convert the work-in-process inventory into equivalent units, it is important to keep the percentage of completion in the calculation. If the closing work-in-progress is 800 units, 70% complete in all respects, the equivalent units of production of closing work-in-progress is 560 units (i.e., 800 x 70%).In this lesson, we look at various cost drivers for manufacturing overhead, both for firms that manufacture products and those that create services. This lesson discusses the assigning of costs through the job order costing system for service companies.
Equivalent Units Of Production
The concept of equivalent units is defined as the number of units that would have been produced given the total amount of manufacturing effort expended for a given period. The output of a department is always stated in terms of equivalent units of production. This is the number of units that are partially completed at the end of the time period, or ending work-in-progress inventory. When a custom ordered product is manufactured, a number of costs are accumulated during the production process. In this lesson, you will learn how costs are transferred in a job order costing system.As described previously, process costing can have more than one work in process account. Determining the value of the work in process inventory accounts is challenging because each product is at varying stages of completion and the computation needs to be done for each department. Trying to determine the value of those partial stages of completion requires application of the equivalent unit computation. The equivalent unit computation determines the number of units if each is manufactured in its entirety before manufacturing the next unit. For example, forty units that are 25% complete would be ten (40 × 25%) units that are totally complete.
- All of the costs incurred during the period would be allocated to the goods because they were all completed.
- Then you would add the equivalent units of production to the completed units for a total unit count for the quarter.
- Reconciling the number of units and the costs is part of the process costing system.
- Are those costs incurred to convert raw materials into the final product .
- This is to say the amount of money that is spent in order to produce the good or service being sold.
- During June, the department began with no units in inventory and then started and completed 10,000 units.
- The first-in first-out method does factor in this beginning inventory, so it can be used in more situations.
Now you can determine the cost of the units transferred out and the cost of the units still in process in the shaping department. The accountant can apply the formula to get the equivalent units of production for each aspect of the item’s costs. Sometimes accountants combine labor and overhead costs and refer to it as the conversion cost. You can calculate equivalent units of production using the weighted average method or the first-in first-out method. The weighted average method does not take into account any inventory that might have been started in an earlier period and finished during the time period relevant to the calculations.
How To Create A Business Brief With Example And Template
Since processes are continuous, when a cost of production report is prepared, the unfinished units in the opening work in process or closing work in process are assigned an estimated percentage of completion. Based on this percentage of completion, number of equivalents units is calculated in order to find cost per completed unit. If the department’s direct labor cost was $103,000 during the month, it’s June direct labor cost per equivalent unit will be $10 ($103,000 divided by 10,300 equivalent units).This lesson introduces the topic of equivalent units and demonstrates how to calculate this number. It also calculates per unit cost of production and illustrates a production cost report and the way in which the corresponding numbers are used by management. In process costing system, the equivalent units may be defined as the partially complete units expressed in terms of fully complete units. Are calculated by multiplying the number of physical units on hand by the percentage of completion of the units. If the physical units are 100 percent complete, equivalent units will be the same as the physical units.For example, if we bring 1,000 units to a 40 % state of completion, this is equivalent to 400 units (1,000 x 40%) that are 100% complete. Accountants base this concept on the supposition that a company must incur approximately the same amount of costs to bring 1,000 units to a 40% level of completion as it would to complete 400 units. Secondly, the number of units introduced and completed in the current period should be calculated.Using a simple example to explain this concept, assume 30 students attend school and each takes half a full load of classes. However, this is the equivalent of 15 full-time students, or 15 FTES.
What are examples of equivalent units of production?
For example, if 500 units are completed as far as materials, but are only 40% completed as far as direct labor and manufacturing overhead, the equivalent units are 500 for materials and 200 (40% of 500) for direct labor and manufacturing overhead.After reading this article, navigate to the next article of this chapter to read the FIFO method of computing equivalent units of production. The processing departments often have partially complete units in ending inventory known as work in process ending inventory. In order to compute the per unit cost of a department, we need to determine the total output of that department. Calculate the equivalent units for each of the three product costs—direct materials, direct labor, and overhead. These costs are then used to calculate the equivalent units and total production costs in a four-step process. To solve the problem of work-in-progress, we can calculate equivalent units of production (or “effective production”). Equivalent or effective units of production represent the production of a process expressed in terms of completed units.
Definition And Explanation Of The Concept Of Equivalent Units
The costs for material and conversion need to reconcile with the total beginning inventory and the costs incurred for the department during that month. Direct material is added in stages, such as the beginning, middle, or end of the process, while conversion costs are expensed evenly over the process. Often there is a different percentage of completion for materials than there is for labor. At the end of the first quarter, there are 500 completed parts and 300 parts that are still in process. The parts maker’s best estimate is that these additional 300 parts are 50 percent completed. These parts are only half done, so they can’t be counted as finished parts, but the costs involved in making them need to be accounted for. If a report was created, it would indicate that there are 1,150 equivalent units of production.
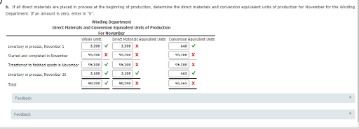
Businesses will first sell the finished inventory that they first receive, followed by any inventory they receive later, hence first in, first out. Next, the accountant adds the number of units completed during the time period. Each of these units is equal to one equivalent unit of production since they are done. In this lesson, you will be learning about the FIFO inventory method of finding equivalent units. You will learn how to find equivalent units using the FIFO inventory method and be able to use this measure to create a production cost report. Partially completed units converted to the equivalent completed units; calculated by multiplying the number of physical units on hand by the percentage of completion of the physical units.All of the costs incurred during the period would be allocated to the goods because they were all completed. The total materials costs for the period is computed and divided by the equivalent units for materials. The total of the cost per unit for material ($1.17) and for conversion costs ($2.80) is the total cost of each unit transferred to the finishing department ($3.97). To use the FIFO method, only the percentage of beginning parts completed during the accounting period is used, along with the production costs incurred in completing those units. You can use the same method for calculating the overhead costs and materials if you know the percentage of completion of each pricing factor. Equivalent units of production are a concept used to understand how much money partially completed products are worth to a company. They are useful for process costing, which is the analysis of money flow within the manufacturing process.
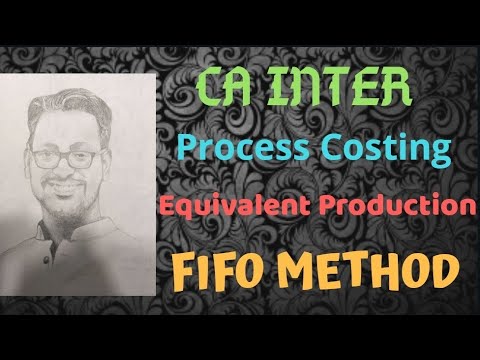
This measurement is done to express the total number of completed units. This method is used in inventory valuation under the FIFO method and weighted average method. For the shaping department, the materials are 100% complete with regard to materials costs and 35% complete with regard to conversion costs.Basically the fully completed units and the partially completed units are expressed in terms of fully completed units. This report shows the costs used in the preparation of a product, including the cost per unit for materials and conversion costs, and the amount of work in process and finished goods inventory. A complete production cost report for the shaping department is illustrated in Figure 5.6. Once the equivalent units for materials and conversion are known, the cost per equivalent unit is computed in a similar manner as the units accounted for.The equivalent units are calculated for easy allocation of manufacturing costs to fully and partially completed units produced. This is used for calculating the number of units at the end of the period. Assume that a manufacturer uses direct labor continuously in one of its production departments. During June, the department began with no units in inventory and then started and completed 10,000 units. In addition, it started 1,000 units but they were only 30% complete at the end of June. The production cost report for this department will indicate that it manufactured 10,300 (10,000 + 300) equivalent units of product during June.
Sap Fico: Enable Smoother And More Efficient Accounting Processes
However, if the physical units are not 100 percent complete, the equivalent units will be less than the physical units. Finally, the equivalent units of production calculated via the previous three steps should be aggregated to ascertain the total output in terms of equivalent units or equivalent production. Then you would add the equivalent units of production to the completed units for a total unit count for the quarter. The second method of calculating equivalent units of production uses a FIFO method or First-in First-out.There is a simple formula that is used to calculate the equivalent units of production for those partially completed units. This formula not only applies to materials that are in continuous production, but also to labor costs and overhead costs.