Content
- Setting The Standards Or Establishing A Standard Costing System
- Introduction To Standard Costing
- Assumes Little Change To The Estimated Costs
- How To Calculate Standard Costs
- Fundamentals Of Standard Costs
- Types Of Standards
The materials are recorded using actual quantity and standard cost. Are costs that management expects to incur to provide a good or service. They serve as the “standard” by which performance will be evaluated. For example, fast-food restaurants have a standard for the length of time it should take to serve a drive-through-window customer.Standard costs have their flaws, but they’re still a useful tool for companies to create an accurate business budget without having to do a ton of complicated math. Coming up with an accurate standard cost does require you to know your product and your team’s capabilities, but even if you start with guesses, you’ll get closer and closer to your actual costs over time. You may even identify ways to improve your profit margins as well. Once you’ve completed the three steps above, the only thing left to do is add up your results from each one. This will give you a standard cost estimate to use as a starting point. Then, as you produce more product, you can update this estimate based on your actual costs to reduce variances. Some of your manufacturing overhead costs may be more or less fixed, such as the property taxes you pay for your warehouses.
Setting The Standards Or Establishing A Standard Costing System
Codes and symbols are assigned to different accounts to make the collection and analysis of costs more quick and convenient. This also helps to analyze variance and, hence, enables managers to be effective in controlling the costs for which they are held responsible.
What are the 4 inventory costing methods?
Types of Accounting Methods There are four accepted methods of costing the items: (1) specific identification; (2) first-in, first-out (FIFO); (3) last-in, first-out (LIFO); and (4) weighted-average. Each method has advantages and disadvantages.For managers within a company, exercising control through standards and standard costs is a creative program aimed at determining whether the organization’s resources are being used optimally. Standard costs provide a high-level view of a company’s production department, but they don’t drill down into specifics. They lack the granularity to show how efficiently your company produced a specific batch or unit of product. Another situation in which a variance may occur is when the cost of labor and/or material changes after the standard was established.For example, ideal standards assume machines never break down, employees are never ill, and materials are never wasted. Although ideal standards may provide motivation for workers to strive for excellence, these standards can also have a negative impact because they may be impossible to achieve. For direct materials represents the final delivered cost of the materials and includes items such as shipping and insurance.
Introduction To Standard Costing
However, in an environment where product lives are short or continuous improvement is driving down costs, a standard cost may become out-of-date within a month or two. To determine the standard for overhead, the coffee shop would first need to consider the fact that it has two types of overhead as shown in Figure 8.2. Greater detail about the calculation of the variable and fixed overhead is provided in Compute and Evaluate Overhead Variances. Is your manufacturing operation using Standard Cost or Actual Cost to value production costs? Are you wondering what the benefits would be if you switched to a Standard Cost valuation of the production of your products? In this blog post, I’ve listed the advantages and disadvantages of using Standard Cost to help with your analysis. Is a carefully predetermined measure of what a cost should be under stated conditions.This is because in the manufacturing process, it is impossible to predict the demand of a product or all the variables that will affect the costs of manufacturing it. Standard costs are estimates of the actual costs in a company’s production process, because actual costs cannot be known in advance.
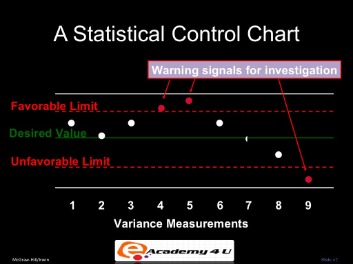
Historical costing, which refers to the task of determining costs after they have been incurred, provides management with a record of what has happened. This is the average market price of your materials multiplied by how many materials you need to produce a single unit.The direct labor efficiency variance is recorded when the direct labor is assigned to work‐in‐process inventory. Firms evaluate management’s and workers’ performances through the use of a budget. When management compares actual results with budgeted amounts, it can see how well it is performing its own duties and managing its employees. Management also can evaluate workers based on how well they performed relative to the budgeted amounts pertaining to the activities they performed. Are formal written plans that represent management’s planned actions in the future and the impacts of these actions on the business. As a business incurs actual expenses and revenues, management compares them with the budgeted amounts.
Assumes Little Change To The Estimated Costs
The balances in the variance accounts are usually closed to the cost of goods sold account, particularly when the amounts are small. Alternatively, the balances in the variance accounts may be allocated to the appropriate inventory accounts and the cost of goods sold account. Another way of computing the direct materials variance is using formulas.Once standards are established, they are used to analyze and determine the reasons for actual cost variances from standards. The variances may be in quantity of materials or hours used to manufacture a product or in the cost of the materials or labor. Because overhead is normally applied on some basis, the variances in overhead will occur because the total overhead pool of dollars or the activity level used to allocate the overhead is different from what was planned. Once standard costs are used in preparing budgets, analysis of variances can be used to provide management with information about whether a variance is caused by quantity or price so that appropriate action can be taken. †Variable overhead costs are applied to products based on direct labor hours.In other companies, engineered standards are being replaced either by a rolling average of actual costs, which is expected to decline, or by very challenging target costs. Instead of recording actual costs for each job, the standard costs for materials, labor, and overhead can be charged to jobs. Usually, effective standards are the result of engineering studies and of time and motion studies undertaken to determine the amounts of materials, labor, and other services required to produce a product. Also considered in setting standards are general economic conditions because these conditions affect the cost of materials and other services that must be purchased by a manufacturing company. A standard cost is one that a company expects at the outset of a year under a normal level of operational efficiency. Standard costs are used periodically as a basis for comparison with actual costs.As we explain next, there are many approaches to establishing these six standards for direct materials, direct labor, and variable manufacturing overhead . Whenever you have set goals that you have sought to achieve, these goals could have been called standards.
How To Calculate Standard Costs
This is because in reality, one batch of a product may cost more to produce than another batch of the exact same product. Maybe there were production delays on the line resulting in staff overtime to finish that second batch. Imagine these types of problems happening all the time, making it very difficult to keep track of the actuals. It is extremely easy to print a report showing the period-end inventory balances , multiply it by the standard cost of each item, and instantly generate an ending inventory valuation. The result does not exactly match the actual cost of inventory, but it is close. However, it may be necessary to update standard costs frequently, if actual costs are continually changing.By looking at the preset costs for operations, management can innovate new ways of producing products that don’t require the same procedures–thus, reducing cost. Historical costs are costs whereby materials and labor may be allocated based on past experience. Predetermined costs are computed in advance on basis of factors affecting cost elements. Within an organization, there are several objectives that a standard costing system may be established to help achieve. Standard cost is used to measure the efficiency of future production or future operations.
Advantages Of Standard Cost
Direct materials are the raw materials that are directly traceable to a product. (In a food manufacturer’s business the direct materials are the ingredients such as flour and sugar; in an automobile assembly plant, the direct materials are the cars’ component parts).
- Most managers feel attainable standards have a positive behavioral impact on workers because the standards are reasonable and attainable under normal production conditions.
- It can be achieved with reasonable effort (i.e., if the company operates with a “high” degree of efficiency and effectiveness).
- Some of your manufacturing overhead costs may be more or less fixed, such as the property taxes you pay for your warehouses.
- If the variance relates to the use of direct labor, it is called the labor efficiency variance.
- Many financial and cost accountants have agreed on the desirability of replacing standard cost accounting.
- The total variance is favorable if the actual costs are less than standard costs.
- Before determining whether the variance is favorable or unfavorable, it is often helpful for the company to determine why the variance exists.
It is unfavorable because more was spent on variable overhead costs per direct labor hour than the $0.72 that was budgeted. Knowing that total variable costs are $5,330 and that 6,500 direct labor hours were incurred, the actual variable overhead costs per direct labor hour rate was $0.82. It occurred because it took only 6,500 direct labor hours instead of 6,650 (13,300 units × .5 hours per unit) direct labor hours to produce the 13,300 units. The total variable cost variance of $542 is calculated by adding the $650 unfavorable spending variance and the $108 favorable efficiency variance.Therefore, if a standard cost estimate turns out to be correct, then the total cost would turn out to be equal to the budget cost. The company could have paid too much or too little for production. It may have purchased the wrong grade of material or hired employees with more or less experience than required. For example, purchasing substandard materials may lead to using more time to make the product and may produce more scrap. The substandard material may have been more difficult to work with or had more defects than the proper grade material. In such a situation, a favorable material price variance could cause an unfavorable labor efficiency variance and an unfavorable material quantity variance.Standard costs are costs management expects to incur to provide a good or service. Manufacturing companies often establish standard costs for direct labor, direct materials, and manufacturing overhead. Standard cost information comes from a number of sources such as historical data, product specifications outlined by product engineers, contracts with suppliers, and labor union contracts. These standard costs can then be used to establish a flexible budget based on a given level of activity. The variable production costs expected to produce these units are shown in the flexible budget in Figure 10.2 “Flexible Budget for Variable Production Costs at Jerry’s Ice Cream”.
Types Of Standards
Toward the end of the fiscal year, standards often become less reliable because time has passed and the environment has changed. It is not reasonable to expect the price of all materials and labor to remain constant for 12 months. For example, the grade of material used to establish the standard may no longer be available. For example, the coffee company mentioned in the opening vignette may expect to pay $0.50 per ounce for coffee grounds. After the company purchased the coffee grounds, it discovered it paid $0.60 per ounce.