Content
- Import Budgeted Hours
- 4 Direct Labor Variance Analysis
- How To Calculate The Direct Labor Budget For The Upcoming Fiscal Year
- What Is The Direct Labor Budget?
- Direct Labor Efficiency Variance Calculation
- Join Pro Or Pro Plus And Get Lifetime Access To Our Premium Materials
How would this unforeseen pay cut affect United’s direct labor rate variance? The direct labor rate variance would likely be favorable, perhaps totaling close to $620,000,000, depending on how much of these savings management anticipated when the budget was first established. The Labor Budget to Actual Report compares the hours recorded in the Timesheets tool to the imported Budgeted Hours at a cost code level. It also summarizes the % of hours used, budgeted hours, actual job-to-date hours, and remaining hours for each project cost code. Although various complex computations can be made for overhead variances, we use a simple approach in this text. In this approach, known as the two-variance approach to variable overhead variances, we calculate only two variances—a variable overhead spending variance and a variable overhead efficiency variance.
How do you find budgeted overhead?
To do this, take your monthly overhead costs and divide it by your company’s monthly sales. Then multiply it by 100. For example, if your company has $100,000 in monthly manufacturing overhead and $600,000 in monthly sales, the overhead percentage would be about 17%.Because of its fixed component, manufacturing overhead tends to be over applied when actual production is greater than standard production. With the insight into your remaining budgeted hours, you’ll be able to quickly assess a project’s current plan and, if necessary, make adjustments on the fly. If you have more Future Scheduled Hours than what remains in your budget, you may need to tighten things up a bit! Conversely, if you’ve got a little wiggle room in your budget, you can add some additional design time to give the project that extra coat of polish. Suggest several possible reasons for the labor rate and efficiency variances. Calculate the labor rate and efficiency variances using the format shown in Figure 10.6 “Direct Labor Variance Analysis for Jerry’s Ice Cream”. BOTH Hourly and Fixed Fee projects include the ability to budget hours for the project.
Import Budgeted Hours
They can view the comparison of ‘Timesheet Hours’ to the budgeted labor hours in a Labor Budget to Actual Report. The primary value of this report is to see the percentage of hours used for each cost code and includes calculated values like remaining and job to date hours. Add the cost of materials to your direct labor costs to find out how much each unit actually costs you to produce.This allows management to anticipate hiring needs, as well as when to schedule overtime, and when layoffs are likely. The budget provides information at an aggregate level, and so is not typically used for specific hiring and layoff requirements. Jerry , Tom , Lynn , and Michelle were at the meeting described at the opening of this chapter.
4 Direct Labor Variance Analysis
Knowing the separate rates for variable and fixed overhead is useful for decision making. The variable overhead rate is $ 2 per machine hour ($ 40,000 variable OH/20,000 hours), and the fixed overhead rate is $ 3 per hour ($ 60,000/20,000 hours).This results in an unfavorable variance since the actual rate was higher than the expected rate. Total overhead variance (2,000 U + 4,000 U + 2,000 U)$8,000 UnfavorableThe unfavorable spending variance is because we had more variable cost per unit than budgeted. The efficiency variance is unfavorable because we spent more machine hours than budgeted because we produced more units. The actual costs would be debited to Manufacturing Overhead and credited to a variety of accounts such as Accounts Payable, Accumulated Depreciation, Prepaid Insurance, Property Taxes Payable, and so on. According to the flexible budget, the standard number of machine-hours allowed for 11,000 units of production is 22,000 hours. Therefore, $ 110,000 of manufacturing overhead is applied to production ($ 5 per machine-hour times 22,000 hours) by debiting Work in Process Inventory and crediting Manufacturing Overhead for $ 110,000.The direct labor budget is typically presented in either a monthly or quarterly format. The basic calculation used by the budget is to import the number of units of production from the production budget and to multiply this by the standard number of labor hours for each unit. This yields a subtotal of the direct labor hours needed to meet the production target. You can also add more hours to account for production inefficiencies, which increases the amount of direct labor hours.Instead, the cash requirements are calculated for all of the revenues and expenditures of a business as a whole, and are then summarized on a separate page of the budget. You must always add your project’s budgeted hours into the provided template XLSX file. Multiply the labor cost for each unit times the total number of units you plan to produce. For example, if you foresee producing 100,000 units, you know your cost will be $3 times 100,000 for a total direct labor cost of $300,000. You may find that it is too time-consuming to create a labor budget in detail when there are many labor classifications, since it is extremely difficult to match the budgeted pay levels to real world staffing. Instead, ongoing turnover in all of the pay classifications will inevitably result in mismatches between what the budget says the company should be paying and what it is actually paying for labor. For each month, project how many units you plan to produce, and multiply by your per-unit labor cost.
How To Calculate The Direct Labor Budget For The Upcoming Fiscal Year
Let’s assume that the budgeted manufacturing overhead for the upcoming year is expected to be $1,000,000 in order to produce the expected 100,000 identical units of product. The standard cost of manufacturing overhead per unit of product is $10 ($1,000,000 divided by 100,000 units). When the products are not identical, the $1,000,000 of manufacturing overhead might be divided by the expected number of machine hours required to manufacture the units of product.
What does flexing the budget mean?
Accounting professionals should be able to ‘flex’ budgets. This process means changing a budget to allow for different sales levels and allows more realistic variance analysis at the end of the financial period in question.In a standard cost system, accountants apply the manufacturing overhead to the goods produced using a standard overhead rate. They set the rate prior to the start of the period by dividing the budgeted manufacturing overhead cost by a standard level of output or activity.
What Is The Direct Labor Budget?
This will show you how much money you need to spend on labor each month of the coming fiscal year. These show that manufacturing overhead has been overapplied to production by the $ 2,000 ($110,000 applied OH – $108,000 actual OH).
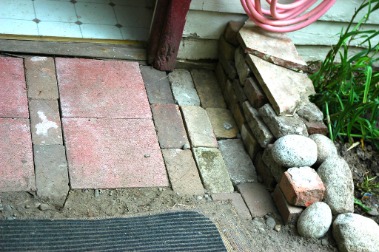
You’ll see the Future Scheduled Hours for each project as a whole, and when a project is expanded, you’ll see the number of hours scheduled for each person assigned to the project. As mentioned earlier, the cause of one variance might influence another variance. For example, many of the explanations shown in Figure 10.7 “Possible Causes of Direct Labor Variances for Jerry’s Ice Cream” might also apply to the favorable materials quantity variance. Add all of the wages you pay per hour, then divide by the number of employees. For example, you might find that your employees earn on average $12 per hour.That is, the variable overhead cost per unit stays constant ($ 2 per machine-hour) regardless of the number of units expected to be produced, and only the fixed overhead cost per unit changes. Since fixed overhead does not change per unit, we will separate the fixed and variable overhead for variance analysis. Managers use a flexible budget to isolate overhead variances and to set the standard overhead rate. Flexible budgets show the budgeted amount of manufacturing overhead for various levels of output. The direct labor budget is used to calculate the number of labor hours that will be needed to produce the units itemized in the production budget. A more complex direct labor budget will calculate not only the total number of hours needed, but will also break down this information by labor category. The direct labor budget is useful for anticipating the number of employees who will be needed to staff the manufacturing area throughout the budget period.
Direct Labor Efficiency Variance Calculation
Then multiply the total number of direct labor hours by the fully burdened direct labor cost per hour to arrive at the total cost of direct labor. As with direct materials variances, all positive variances are unfavorable, and all negative variances are favorable. The labor rate variance calculation presented previously shows the actual rate paid for labor was $15 per hour and the standard rate was $13.Note that both approaches—the direct labor efficiency variance calculation and the alternative calculation—yield the same result. Note that both approaches—direct labor rate variance calculation and the alternative calculation—yield the same result. Is the difference between the actual number of direct labor hours worked and budgeted direct labor hours that should have been worked based on the standards. The difference between the actual number of direct labor hours worked and budgeted direct labor hours that should have been worked based on the standards. The budget contains two types of labor that are compiled separately, since they have different costs. There are 0.1 machine hours of time required for each product manufactured, which costs the company $25 per hour. Additionally, there are 0.05 other hours of time required for each product manufactured, which costs the company $15 per hour.
- It is defined as the difference between the actual number of direct labor hours worked and budgeted direct labor hours that should have been worked based on the standards.
- The variable OH efficiency variance shows whether plant assets produced more or fewer units than expected.
- This will show you how much money you need to spend on labor each month of the coming fiscal year.
- To import budgeted hours to set up a Labor Budget to Actual Report that shows a comparison of labor hours to budgeted hours for each cost code in the project.
The labor efficiency variance calculation presented previously shows that 18,900 in actual hours worked is lower than the 21,000 budgeted hours. Clearly, this is favorable since the actual hours worked was lower than the expected hours. Note that the difference in rates is due solely to dividing fixed overhead by a different number of machine-hours.As shown in the following, the labor rate variance is $ favorable, and the labor efficiency variance is $234,000 unfavorable. The 21,000 standard hours are the hours allowed given actual production. For Jerry’s Ice Cream, the standard allows for 0.10 labor hours per unit of production. Thus the 21,000 standard hours is 0.10 hours per unit × 210,000 units produced. This feature allows users to upload budgeted labor hours from outside the Budget tool.
Possible Causes Of Direct Labor Variances
If your Forecast account is linked to a Harvest account, any linked project with an hourly budget that doesn’t reset in Harvest will display the remaining budgeted hours below its Future Scheduled Hours. Projects with fee-based budgets or with hourly budgets that reset monthly in Harvest and unlinked projects won’t display this figure. Instead, they’ll display N/A, and you can hover over this text to surface the reason.Enter the number of budgeted hours estimated for each cost code in the Labor Hourscolumn . In the Beta Company illustration, the budgeted fixed overhead was $60,000 and the actual fixed costs were $62,000. A budget usually refers to a department’s or a company’s projected revenues, costs, or expenses. A standard usually refers to a projected amount per unit of product, per unit of input , or per unit of output. Check the import and verify that all budgeted hours entered in the Labor Hours column were properly imported by viewing them on the Unit Quantity Based Budget page or in the Labor Budget to Actual Report. The system downloads a copy of the project-name-import-unit-quantity-based-budget.xlsxfile to the download location for your web browser. When looking at the Projects section of your schedule, click the clock icon in the title bar to view the Future Scheduled Hours in your Forecast account.