Content
- Measure Costs Right: Make The Right Decisions
- Managerial Accounting
- How To Handle Support Costs And Overhead
- Learn How Fixed Costs And Variable Costs Affect Gross Profit
- Managerial Accountant’s Role In Business Planning
- Direct Material Costs
Plant II might consider dropping its prices on blue pens. Financial accounting treats R&D as a cost of the period in which it takes place. The management accounting system, in contrast, should treat these costs as investments in the future. Companies engaged in extensive R&D for products with short life cycles should measure costs and revenues over the life cycle of their products. Any periodic assessment of product profitability will be misleading, since it depends on the arbitrary amortization of investment expenditures including R&D. Similarly, companies engaged in major product development and process improvements should attribute the costs of design and engineering resources to the products and product lines that benefit from them. Otherwise, product and process modification costs will be shifted onto product lines for which little development effort is being performed.
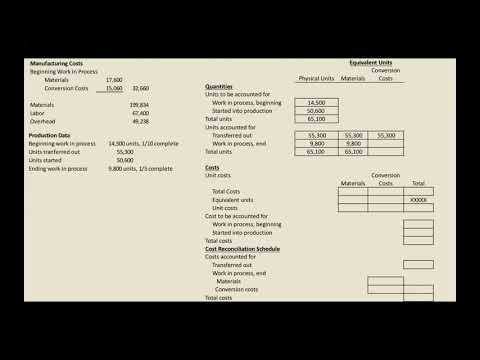
A good system yields unit costs for all key activities , and it includes the unit costs of transactions like setups, shipments, part and vendor quantities, and inspections. A company can estimate a new product’s cost by specifying its demands on both activities and transactions. Decisions regarding product introduction, abandonment, and pricing are strategic matters that should be based on the long-run marginal costs of each product. For operations under computer control, the digital data can be captured to record what, when, and how much was produced. Companies no longer need to collect production data with stopwatches, time clocks, and clipboards. Automatic bar-code reading of parts combined with local area networks permit continual tracking of parts and operations.
Measure Costs Right: Make The Right Decisions
In the latter case, product cost should include all costs related to a service, such as compensation, payroll taxes, and employee benefits. Activity-based costing is not designed to trigger automatic decisions. It helps managers make better decisions about product design, pricing, marketing, and mix, and encourages continual operating improvements. Production costs refer to all of the direct and indirect costs businesses face from manufacturing a product or providing a service. Production costs can include a variety of expenses, such as labor, raw materials, consumable manufacturing supplies, and general overhead. The product cost system can ignore only two classes of costs—expenses incurred that benefit future products, like basic research or development, and the expenses of idle or unused capacity. Existing financial accounting rules require that basic R&D be expensed each period.Others, recognizing the declining role of direct labor, use two additional allocation bases. Materials-related expenses are allocated directly to products as a percentage markup over direct materials costs. And machine hours, or processing time, are used to allocate production costs in highly automated environments. Cost accounting analyzes a company’s total production costs for its products or services. A form of management accounting, cost accounting examines all variable and fixed expenses and is meant for internal eyes only. Company decision-makers use the results to identify which products and services are most profitable and which ones cost too much to produce relative to sales.A lower per-item fixed cost motivates many businesses to continue expanding production up to its total capacity. This allows the business to achieve a higher profit margin after considering all variable costs. Full costing is a managerial accounting method that describes when all fixed and variable costs are used to compute the total cost per unit. Production incurs both fixed costs and variable costs.De-emphasize blue pens and offer an expanded line of differentiated products with unique features and options. Consider the experience of a leading manufacturer of hydraulic valves whose product line included thousands of items. About 20% of the valves generated 80% of total revenues, a typical ratio for multiproduct organizations. Of even greater interest, 60% of the products generated 99% of the revenues. Nonetheless, management remained enthusiastic about the 40% of its products that generated only 1% of revenues. According to its cost system, these specialty items had the best gross margins. The cost of direct materials placed into production during the month .
Managerial Accounting
Production incurs both direct costs and indirect costs. Direct costs for manufacturing an automobile, for example, would be materials like plastic and metal, as well as workers’ salaries. Indirect costs would include overhead such as rent and utility expenses. Total product costs can be determined by adding together the total direct materials and labor costs as well as the total manufacturing overhead costs.
How costing method help the producer of product?
Costing allows the business to attach specific costs not only to products but to product materials, features and abilities that allow for highly accurate manufacturing cost predictions.And the expense of collecting and processing data made it hard to justify more sophisticated allocation of these and other indirect costs. Production costs, which are also known as product costs, are incurred by a business when it manufactures a product or provides a service. For example, manufacturers have production costs related to the raw materials and labor needed to create the product. Service industries incur production costs related to the labor required to implement the service and any costs of materials involved in delivering the service. Direct costs are related to the production/acquisition of products or delivery of services. For a manufacturer, these would include the raw materials and parts that go into a final product, as well as the labor involved in its production. For some services-based businesses, such as a law firm, labor may be the only direct cost.
How To Handle Support Costs And Overhead
After several years of bickering, the company overhauled the new system to recapture the old system’s output. The sidebar “Allocating Costs under an Activity-Based System” shows how a company might calculate and assign the support costs of a common manufacturing overhead function—raw materials and parts control.Scaling back on blue pens and replacing the lost output by adding new models will further increase overhead. Plant II’s managers will simmer with frustration as total costs rise and profitability goals remain elusive. An activity-based cost system would not generate distorted information and misguided strategic signals of this sort. A total of 6,000 units of product remain in the Quality Testing department at the end of the year. Direct materials are 75 percent complete and direct labor is 20 percent complete.
What is product cost with example?
Examples of Product Costs and Period Costs Examples of product costs are direct materials, direct labor, and allocated factory overhead. Examples of period costs are general and administrative expenses, such as rent, office depreciation, office supplies, and utilities.If 500 mountain bikes are sold in April, their cost to manufacturer is recognized in April, too. Unlike the labor efficiency variance, the variable overhead efficiency variance considers indirect costs, such as the salaries of office staff and site security.
Learn How Fixed Costs And Variable Costs Affect Gross Profit
For example, an orange juice company management will track the price of oranges, sugar, and othercommoditiesused in the production of their juice. If any of these goods’ prices increase, the juice manufacturer will also have to increase their prices to maintain the same level of profits. Factory overhead consists of those costs required to maintain the production function, but which are not directly consumed on individual units. Examples are utilities, insurance, materials management salaries, production salaries, maintenance wages, and quality assurance wages. A factory’s production costs are the total expenses of doing business.According to labor- and materials-based cost accounting, these items had the best gross margins. But activity-based costing revealed that 75% of the company’s products were losing money. “Valve 3” was thought to have a 47% gross margin; in fact, the company would have done better to mail its customers cash to buy the valve elsewhere.Even corporate expenses should be allocated to product costs, especially if they vary across lines. They can vary by risks of product liability and environmental damage, or by antitrust concerns across different categories of products. Companies measure performance by comparing actual results against standard or budgeted levels. Comparisons can be made periodically or each time a unit of work is finished.
- Cost accounting looks at the cost to produce or deliver goods/service.
- A form of management accounting, cost accounting evaluates a company’s total costs to produce its products or services and is meant to be used by internal stakeholders only.
- Otherwise, product and process modification costs will be shifted onto product lines for which little development effort is being performed.
- Nonetheless, additional production always generates additional manufacturing costs.
- Executives of multiproduct companies will be fortunate if the first digit in their product cost estimates is valid, and they can make a reasonably good guess at the second.
- The price for blue pens is lower than for lavender pens, but the cost system reports that blue pens are as expensive to make as the lavender.
An effective system to measure product costs must identify and assign to products these costs of complexity. They might also consider switching to activity-based costing to match costs to products more accurately. Cost accounting analyzes a number of “input” costs — namely, material, labor and overhead — related to the production of a product or service, and there are efficiency variance formulas for each. The resulting variance highlights the difference between the two and can be key to effective cost control.Calculate the equivalent units in the Assembly department for direct materials and direct labor. In this example, the total production costs are $900 per month in fixed expenses plus $10 in variable expenses for each widget produced. To produce each widget, the business must purchase supplies at $10 each. After subtracting the manufacturing cost of $10, each widget makes $90 for the business. Here’s an example of cost accounting for a typical small manufacturing company we’ll call “Bellmore Gizmos.” The company produces a variety of widgets, but they all have roughly the same costs of production. Bellmore Gizmos uses standard cost accounting, which means overhead costs are allocated across the entire production.Cost accounting figures are used only by a company’s internal management team, so collection methods can be customized according to company needs. Cost accounting informs budgeting decisions, product/service pricing and business strategy.
Managerial Accountant’s Role In Business Planning
These costs include direct labor,direct materials, consumable production supplies, and factory overhead. Product cost can also be considered the cost of the labor required to deliver a service to a customer.
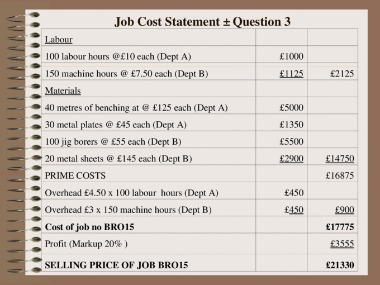
Cost accounting helps companies identify areas where they may be better able to control their costs, as well as set or adjust pricing to maintain profitability. While the typical operational control system segregates costs incurred at each responsibility center, a good product cost system should report expenses incurred across the organization’s entire value chain. The board of directors at Computer Tech established a compensation incentive plan that includes a substantial bonus for the president of the company if annual net income before taxes exceeds $2,000,000.Direct labor costs incurred during the month but not yet paid . Products with a cost of $100,000 are completed and transferred from the Packaging department to the finished goods warehouse. Direct materials totaling $80,000 are requisitioned and placed into production—$60,000 for the Mixing department, $11,000 for the Testing department, and $9,000 for the Packaging department. Products with a cost of $35,000 are completed and transferred from the Packaging department to the finished goods warehouse. Direct materials totaling $15,000 are requisitioned and placed into production—$7,000 for the Fabrication department and $8,000 for the Packaging department. With keyboards selling at $30 in store, and even more for a custom-built keyboard, he sees that the firms still has a reasonable cushion for profit.Some companies aren’t even aware that they’re relying on distorted information about their costs, margins, and profits. The accounting systems they’re using were designed for companies that manufactured a narrow range of products, and for whom materials and direct labor represented the most significant costs.
Direct Material Costs
Cost control systems can record these data and provide frequent, accurate reports on actual output and resource consumption. Once executives are armed with more reliable cost information, they can ponder a range of strategic options. Many low-volume products have surprisingly low price elasticities. Customers who want lavender pens or valve 3 may be willing to pay much more than the current price. On the other hand, these customers may also react to a price increase by switching away from low-volume products. That too is acceptable; the company would be supplying fewer money-losing items.