Content
- What Is The Job Order Costing System?
- Helps You Monitor The Fixed Assets:
- Documents For Job Order Costing Systems
- Law Firms And Accounting Businesses
- Job Cost Sheet
Due to the practical difficulties of using actual costing, many companies instead utilize a normal costing system to obtain a close approximation of the costs on a timelier basis, especially manufacturing overhead costs. Direct materials and direct labor are much more feasible in terms of access to actual costs from materials requisition forms and labor time sheets, while manufacturing overhead costs pose difficulties in determining actual costs. Companies that mass produce a product allocate the costs to each department and use process costing. For example, General Mills uses process costing for its cereal, pasta, baking products, and pet foods. Job order systems are custom orders because the cost of the direct material and direct labor are traced directly to the job being produced. For example, Boeing uses job order costing to manufacture planes.
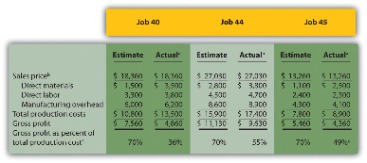
Overhead CostsOverhead cost are those cost that is not related directly on the production activity and are therefore considered as indirect costs that have to be paid even if there is no production. Examples include rent payable, utilities payable, insurance payable, salaries payable to office staff, office supplies, etc.
What Is The Job Order Costing System?
The actual cost to produce each unit through a process costing system varies, but the average result is an adequate determination of the cost for each manufactured unit. Product Costs Similarities Product costs consist of direct materials, direct labor, and manufacturing overhead. Differences Process Costing Job Costing Product costs are assigned to departments . Unit Cost Information Similarities Unit cost information is needed by management for decision-making purposes. Differences Process Costing Job Costing Unit cost information comes from the departmental production cost report.In order to calculate accurately, we will need materials, direct labor, and factory overhead costs. A process costing system is used by companies that produce similar or identical units of product in batches employing a consistent process.Overhead costs are all of those costs that a business incurs that cannot be directly related to a particular product. Remember our discussion about indirect costs—these costs fall into our overhead. If you aren’t charging separate shipping fees, you’ll need to include those as well, whether you choose to mail the product or deliver it on company trucks. One of these expenses in this example is the software your customers used to place their orders and create their t-shirt design. This costs you $5,000 a year to run, but you can’t charge one customer for that amount, so you need to break it down into a rate you can charge per order. Not only does each product your company produces require materials, but it also requires man-hours. Again, though, make sure you aren’t just calculating the obvious hours that went toward producing a product; be sure to note the work that went in behind the scenes as well.
Helps You Monitor The Fixed Assets:
Now you can develop a training course to make them perform better and it will eventually increase the performance of your business. With the help of the job order costing method, management can ascertain which job is profitable, which is not. Cost CenterCost center refers to the company’s departments that don’t contribute directly to the corporate revenue; however, the firm has to incur expenses for keeping such units operative. It comprises research and development, accounting and human resource departments. Identify whether each business listed in the following would use job costing or process costing. In the first stage of production, Coca-Cola mixes direct materials—water, refined sugar, and secret ingredients—to make the liquid for its beverages.
What type of industry is likely to use a job order cost system give some examples?
Examples of industries that use job order systems are custom home builders, commercial printing companies, motion picture companies, construction contractors, repair shops, accounting and law firms, hospitals, shipbuilders, and architects.Calculating the overhead cost is the most difficult part because you will have to rely on an estimation instead of an exact figure. If your kitchen renovation company contracts with designers instead of hiring an in-house team, for instance, the amount you pay those contractors for the project is an example of a direct expense you’d need to account for. In this article, we will discuss the Job Order Costing System and explain how it actually works.
Documents For Job Order Costing Systems
Job order costing tracks prime costs to assign direct material and direct labor to individual products . Process costing also tracks prime costs to assign direct material and direct labor to each production department . Manufacturing overhead is another cost of production, and it is applied to products or departments based on an appropriate activity base. Used in a specific job is identified and added to the cost of production. Direct labor cost is calculated based on no. of manpower and no. of hours worked. If the specific job is related to providing service, then direct labor cost is comprised of almost 80% – 90% of the total cost.
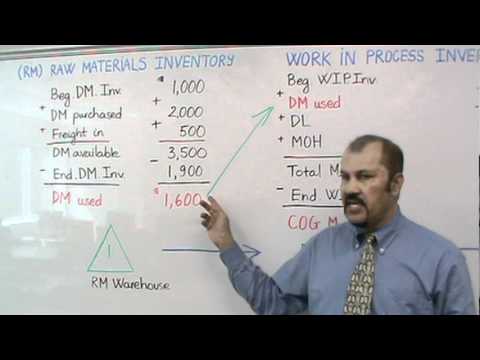
This process allows companies to allocate all of the costs incurred in a business, whether direct or indirect to jobs. We will discuss service and manufactured jobs, and follow a couple jobs from the beginning to end. In order to calculate the cost of these elements for an individual project, you’ll need to start by estimating your total overhead for the year. Once you have that, you can divide it by your estimated number of machine or labor hours for the year. Job order costing is a system for determining the cost of each individual product a company provides for a customer, whether that product is a service or a physical item.
Law Firms And Accounting Businesses
JuneActual Factory Overhead Costs$6,000$12,000Actual Direct Labor Hours15,000 hrs.20,000 hrs.During this two-month period, one customer sent in an identical order each month, calling for the production of 1,000 units. This required 400 direct laor hours at $1 per hour and materials amounting to $750. The Moon Manufacturing Co. has a partial job order costing system instead of predetermining a factory overhead rate. Examples of service businesses that use job order costing system include movie producers, accounting firms, law firms, hospitals etc. In film studios, job order costing is used to track employee salaries as well as the cost of props, costumes, set location and filming equipment. Some film studios also use job sheets as estimates to determine how much it will cost to purchase each item and hire each employee in order to build a specific budget for each film.This means that the company would estimate $6 in manufacturing overhead costs for every one machine hour worked. So, if the company actually worked 5000 machine hours, the estimated overhead costs would be $30,000. Job order costing systems can gain and track information from financial resources like material costs, payroll records, supplier invoices and overhead allocations.
- Once the total overhead cost has been calculated, it is then divided between the production based on whichever allocation base the company has determined most effective.
- Learn accounting fundamentals and how to read financial statements with CFI’s free online accounting classes.
- You can also choose margins for these materials to cover other costs including delivery or clearing costs.
- Since there are eight slices per pizza, the leftover pizza would be considered two full equivalent units of pizzas.
- A cost comparison is difficult because, in this method, the cost sheet is prepared for each job separately according to the specification.
- We will talk a bit more about that shortly, but for now, know that is a place where we “hold” the amounts as they are incurred.
Since this order is unique, a business would use job order costing to create a unique price to charge the customer for their custom-made shoe. These general rules for S&A expenses, however, have their exceptions. For example, some items that are classified as overhead, such as plant insurance, are period costs but are classified as overhead and are attached to the items produced as product costs. Job order costing becomes crucial when customers place orders for different products or services from a particular company or business. Job order costing is useful only for those organizations which are work based on customer requirements, and one job is different from another so that cost of each job can be calculated. Still, it is vital to identify all the cost which is incurred in the completion of a job otherwise it will be lost to the company because the cost of one job cannot be assigned to another job. It is a costly affair because it requires skills and knowledge for identifications of cost, analysis, and controls the cost.The company computes a separate factory overhead rate at the end of each month. This rate is used to charge the factory overhead to the jobs worked on during the month. The number of direct labor hours used on the jobs is the basis of such allocation. This helps an accountant keep better track of the money spent on each item and the current inventory to prevent unexpected losses from occurring. Job order costing is a costing method that is used for determining the production cost of each product. If a business or company produces different and unique products for customers then the business might need a job order costing system to properly manage each product and order. Are those cost which is incurred in the manufacturing of a product or providing service other than the direct labor and direct material like Rent, Electricity, Depreciation, Legal Fees and any other.
Job Order Costing
It helps the business or company to execute more accurate estimations for similar projects in the future based on their past reports. It helps to find the manufacturing cost of each project to determine whether it is making profits or going into loss. This basically works in favor of the business to decide whether they have to make changes or not. Getting accurate information about the manufacturing costs will allow you to understand the potential profits and help you decide how much you have increased or decreased the production cost to meet your goals. They usually use the database to help you track the production cost of each item or service. Later you can use that information to make changes to the production cost that eventually leads to profit. They mainly depend on the expertise of the production manager.
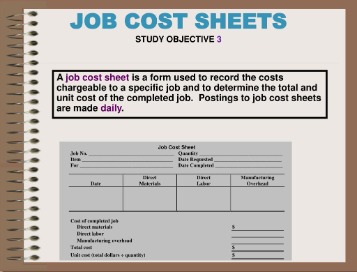
How manufacturers group jobs depends on the size of the company. For example, a small business manufacturer may consider any job valued over $1,000 as a single job, but they may group smaller customer orders together in blocks of $1,000 for costing purposes. With processing, it is difficult to establish how much of each material, and exactly how much time is in each unit of finished product.
Business In Action 4 1
Therefore, a person who is allocating cost to a specific job must have knowledge; otherwise, a small mistake can change the cost of the product. A cost comparison is difficult because, in this method, the cost sheet is prepared for each job separately according to the specification. In this type of cost, each job has done against customer orders only, not as a regular production.In job order cost production, the costs can be directly traced to the job, and the job cost sheet contains the total expenses for that job. Process costing is optimal when the costs cannot be traced directly to the job. For example, it would be impossible for David and William to trace the exact amount of eggs in each chocolate chip cookie. It is also impossible to trace the exact amount of hickory in a drumstick.
Job Cost Sheet
Even two sticks made sequentially may have different weights because the wood varies in density. These types of manufacturing are optimal for the process cost system. Manufacturing departments are often organized by the various stages of the production process. Each department, or process, will have its own work in process inventory account, but there will only be one finished goods inventory account. In this chapter, you will learn when and why process costing is used. You’ll also learn the concepts of conversion costs and equivalent units of production and how to use these for calculating the unit and total cost of items produced using a process costing system. Therefore, there is a chance of excess/shortage allocation of cost.Using a job order costing system can help ensure the time and resources you’re using to build a product will bring in a profit for your business. Building a job order costing system involves different elements to ensure the accuracy of each job’s cost. When a company mass produces parts but allows customization on the final product, both systems are used; this is common in auto manufacturing. Each part of the vehicle is mass produced, and its cost is calculated with process costing. However, specific cars have custom options, so each individual car costs the sum of the specific parts used. Since there are eight slices per pizza, the leftover pizza would be considered two full equivalent units of pizzas. The equivalent unit is determined separately for direct materials and for conversion costs as part of the computation of the per-unit cost for both material and conversion costs.